Background: The Challenges of Marine Environments
The marine environment is exceptionally challenging due to its inherent harsh conditions. Saltwater, humidity, and extreme temperatures subject materials to accelerated wear and tear. Corrosion is a major issue, causing metal parts to weaken over time and potentially fail. Other common problems include material fatigue and ongoing maintenance challenges, which amplify operational costs.
To ensure integrity and reliability in marine applications, fastening systems must be meticulously chosen. Dependable fastening solutions significantly reduce maintenance requirements and prolong service life, keeping vessels and structures secure even under severe maritime conditions.
About Manufacturer’s 304 Stainless Steel Self-Tapping Screws
Manufacturer’s 304 stainless steel self-tapping screws are designed specifically to withstand tough environments like those seen in marine settings. These screws are composed primarily of chromium and nickel, providing excellent corrosion resistance while maintaining strength.
A key feature of these screws is their self-tapping capability, allowing them to form threads as they penetrate a material. This greatly simplifies the installation process and reduces the need for pre-drilling, saving valuable time on projects.
The high resistance to rust and degradation makes 304 stainless steel an ideal choice for marine applications where exposure to saltwater and humidity is inevitable. These screws maintain their structural integrity even after prolonged exposure, ensuring lasting performance.
Field Testing and Methodology
For thorough validation, field tests were conducted at various locations with diverse marine conditions. Sites were selected based on factors such as salinity levels, temperature ranges, and exposure duration.
The installation process was methodically documented, outlining the specific steps and tools used to insert the screws into different substrates typically encountered in marine engineering. Performance data was collected through both visual inspections and lab-based evaluations to track signs of corrosion and structural stability over time.
Performance Metrics and Results
Visual inspections revealed that the screws exhibited minimal surface rust even after extended periods submerged in salty conditions. Lab tests confirmed this finding, showing no significant metallurgical changes.
In terms of load-bearing capabilities, assessments demonstrated sustained structural integrity. The screws retained their hold without loosing or compromising the joined materials, affirming their suitability for critical applications.
Long-term durability studies concluded positively, highlighting that Manufacturer’s 304 stainless steel screws could effectively endure years of marine exposure with consistent performance.
Comparing to Other Fastening Solutions
Other popular materials for marine fasteners include brass and galvanized steel. While brass offers decent corrosion resistance, it lacks the hardness needed for certain structural tasks. Galvanized steel, though sturdy, is prone to eventual rust when coatings degrade.
Compared to these alternatives, Manufacturer’s 304 stainless steel self-tapping screws showed superior longevity and cost-effectiveness. Initial investment may be higher than cheaper counterparts, but reduced maintenance costs and long-lasting resilience result in lower total ownership costs over time.
Real-World Applications
Several real-world cases underscore the efficacy of these screws. In one project, marine engineers used them to assemble dock components, reporting seamless installation and enhanced robustness against constant wetness. Another example saw contractors fixing hull panels, praising the screws' ability to sustain heavy loads without loosening.
Feedback from professionals has been highly favorable, noting fewer repairs and replacements, translating to marked maintenance savings.
Practical Tips for Using Self-Tapping Screws in Marine Settings
For optimal application, it's recommended to install these screws using appropriately sized pilot holes and torquing them to specified limits to avoid overdriving. Regular checks are advisable to detect early signs of wear. Lubricating screws during installation can help prevent galling and ease future removal if necessary.
If facing issues like backing out due to vibrations, consider using locking mechanisms such as thread lockers or lock washers.
Future Prospects and Innovations
Emerging technologies aiming to enhance performance in corrosive environments include advanced polymer coatings and composite materials. Manufacturer is currently exploring these advancements alongside improving existing product lines.
Industry trends indicate a growing reliance on sustainable and durable fastening methods, reinforcing the relevance of high-performance options like Manufacturer's 304 stainless steel self-tapping screws.
Additional Resources
For further information, technical datasheets detailing specifications and comprehensive performance metrics are available. Step-by-step installation guides and video tutorials provide practical assistance, ensuring best results from Manufacturer’s product range.
For inquiries or support, contact Manufacturer through their official channels listed on their website.
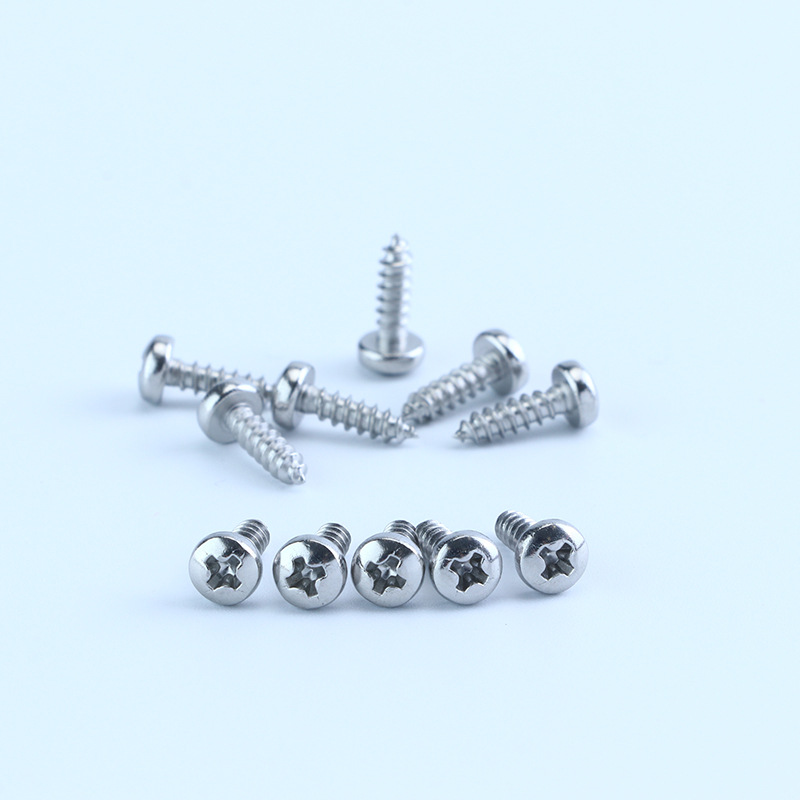